<문제>
<전체 정답>
11243 / 24242 / 34331 / 11333
<해설>
1. 알루미늄 합금의 인장 실험에 대한 설명으로 가장 옳지 않은 것은?
① 진변형률(true strain)이 공학적 변형률(normal strain) 보다 크다.
② 항복점(yield point) 이후 변형경화로 인해 진응력이 증가한다.
③ 변형률속도(strain rate)가 증가할수록 강도가 증가한다.
④ 진응력-진변형률곡선의 아랫부분 면적에 해당하는 인성(toughness)의 단위는 [J/m³]와 같다.
답 : ①
인장 시험에서 진변형률이 공학적 변형률(공칭변형률)보다 작다.
인장시험 - 진응력>공칭응력, 진변형률<공칭변형률
압축시험 - 진응력<공칭응력, 진변형률>공칭변형률
2. 절삭가공에서 사용되는 공구용 재료에 대한 설명으로 가장 옳지 않은 것은?
① 고속도강은 충격을 받는 단속 절삭에는 적합하지 않다.
② 입방정 질화 붕소(cubic boron nitride, CBN) 공구는 다이아몬드 다음으로 높은 수준의 고경도를 가지고 있다.
③ 초경합금공구는 분말 야금법을 통해 만들어진다.
④ 다이아몬드의 강한 화학적 친화성 때문에 일반탄소강의 가공에는 적용이 어렵다.
답 : ①
고속도강은 충격에 강하다.
다이아몬드, 초경합금, 세라믹 공구는 충격을 받는 단속 절삭에는 적합하지 않다.
② 절삭공구의 경도순서 : 다이아몬드>CBN>세라믹>서멧>초경합금>고속도강>탄소공구강
3. 셸 몰드법(shell molding)에 대한 설명으로 가장 옳지 않은 것은?
① 주형 제작을 위해 금속 원형이 사용된다.
② 주형 재료로는 규사와 열가소성 수지의 혼합물인 레진 샌드(resin coated sand)를 사용한다.
③ 셸(shell) 형태로 제작된 2개의 셸을 접합하여 주형으로 사용한다.
④ 표면이 깨끗하고 정밀도가 높은 주물을 얻을 수 있는 주조법이다.
답 : ②
셸 몰드법 - 규사와 열경화성 수지를 배합한 레진 샌드를 가열된 모형에 융착시켜 만든 셀형태의 주형 사용
4. 소모성 주형과 영구 패턴(모형)을 사용하는 주조 공정에 해당하지 않는 것은?
① 사형 주조(sand casting)
② 세라믹 주형 주조(ceramic-mold casting)
③ 석고 주형 주조(plaster-mold casting)
④ 인베스트먼트 주조(investment-casting)
답 : ④
인베스트먼트 주조는 왁스, 파라핀 등에 내열제를 코팅한 모형을 사용한다.
5. 금속의 정수압 압출(hydrostatic extrusion)의 특징에 대한 설명으로 가장 옳지 않은 것은?
① 용기와 빌릿 간 마찰이 작용하지 않는다.
② 다이(die) 구멍에서의 마찰을 줄일 수 있다.
③ 램 압출력은 직접압출에 비해 다소 증가한다.
④ 초기 빌릿의 한 쪽에 테이퍼를 만들어 다이 입구에 꼭 맞게 해야 한다.
답 : ③
램 압출력은 직접압출이 가장 크다.
6. 고상용접(solid phase welding)에 대한 설명으로 가장 옳지 않은 것은?
① 부품 표면의 접합이 압력 단독으로 혹은 열과 압력으로 얻어진다.
② 용가재 금속이 사용된다.
③ 두 표면 사이에서 화학적인 박막과 기름이 존재하면 정상적인 물리적 접촉이 일어나기 어렵다.
④ 단접, 롤 용접 및 확산 용접이 고상용접 공정에 포함된다.
답 : ②
고상용접에는 용가재를 사용하지 않는다.
피복금속아크용접에서 금속 용가재, 납접에서 땜납(solder) 용가재를 사용한다.
7. 금속박판가공 중 드로잉(drawing)에 대한 설명으로 가장 옳지 않은 것은?
① 블랭크 홀더의 고정력이 너무 작으면 플랜지부에 주름이 발생한다.
② 형상변화가 심하면 재드로잉을 수행해야 한다.
③ 얇은 박판일 경우 플랜지부에 주름이 발생하기 쉽다.
④ 금속박판과 블랭크 홀더부의 마찰을 최소화하여야 한다.
답 : ④
금속박판과 블랭크 홀더부의 마찰이 너무 작으면 드로잉이 진행되지 않는다.
- 순수드로잉 : 블랭크홀더 지지력이 작으면 소재가 다이공동부로 빨려들어가 직경이 줄며 드로잉 진행
- 네킹(necking, 파단) : 블랭크홀더 지지력이 너무 클 때
- 다이-펀치 간극이 작으면 아이어닝효과, 너무 작으면 펀치에 의해 천공, 전단
- 다이-펀치 모서리반경이 너무 작으면 모서리부에서 파단
- 다이-펀치 모서리반경이 너무 크면 주름 발생
- 드로우비드(draw bead) : 지지력 역할. 불균질 유동하는 각통‧비축대칭 가공시 필수
- 커핑(cupping) : 컵의 형상으로 가공. 단일공정
- 아이어닝(ironing) : 다이공동부로 빨려들어가는 판재 두께가 펀치-다이 간극보다 크면 두께가 얇아지면서 길어진다. 측벽이 균일하고 매끄럽게 된다.
- 역드로잉 : 1차드로잉과 반대로 드로잉. 제품의 내외측이 바뀌며 연신율↑(바우싱거 효과)
- 재드로잉 : 1차드로잉과 같은방향으로 드로잉. 제품의 내‧외측 그대로.
8. 압연 공정에 대한 설명으로 가장 옳지 않은 것은?
① 소재에 압연 방향으로 장력을 가하면 압하력이 감소한다.
② 압하율이 작은 경우 소재의 표면에 인장잔류응력이 남는다.
③ 롤과 소재의 접촉면에서 중립점은 마찰이 작을수록 출구점에 가까워진다.
④ 소재 표면의 마찰력은 중립점을 경계로 반대방향으로 작용하나, 크기분포는 서로 다르다.
답 : ②
압연에서 압하율이 작은 경우 표면에서 압축응력, 중심에서 인장응력이 발생하고, 반대로 압하율이 클 경우 표면에서 인장응력, 중심에서 압축응력이 발생한다.
① 압연 시 압하력이 감소하는 경우 : 지름이 작은 롤 사용, 패스당 압하율 감소, 작은 마찰, 높은 판재온도, 전/후방 장력
③ 아래 그래프는 입구점(x=0)에서 출구점(x=L)까지의 압연압력을 나타낸 것이다. 마찰계수가 작을수록 압연압력이 최대가 되는 점(=중립점)이 출구쪽으로 이동하는 것을 볼 수 있다.
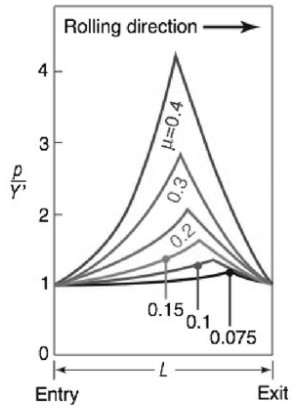

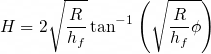
(p_in : 입구측~중립점까지의 압력, p_out : 중립점~출구측까지의 압력, Y' : 소재의 항복응력, h : 소재두께, h_o : 입구측에서 소재두께, h_f : 출구측에서 소재두께, R : 롤 반지름, φ : 수직축으로부터 접촉점까지의 각도, μ : 마찰계수)
④ 소재 표면의 마찰력은 중립점 이전에서는 소재를 압연방향으로, 중립점 이후에서는 소재를 압연 반대 방향으로 밀어내는 방향으로 작용한다. 그러나 마찰력의 크기 분포(φ, h값을 변수로 하는 지수함수 모양)는 중립점을 경계로 대칭적이지 않고 입구측~중립점에서와 중립점~출구측에서 서로 다르다. 압연력 P는 압연압력 p에 접촉면적을 곱한 값이고 마찰력 F는 압연력 P에 마찰계수 μ를 곱한 값이다.(F=μP) 위 그래프에서 압연압력은 중립점에서 최대이나 중립점을 기준으로 분포가 대칭적이지 않음을 알 수 있다. 마찬가지로 압연력과 마찰력 역시 중립점을 기준으로 분포가 대칭적이지 않다(=중립점을 기준으로 크기분포가 서로 다르다)고 할 수 있다.
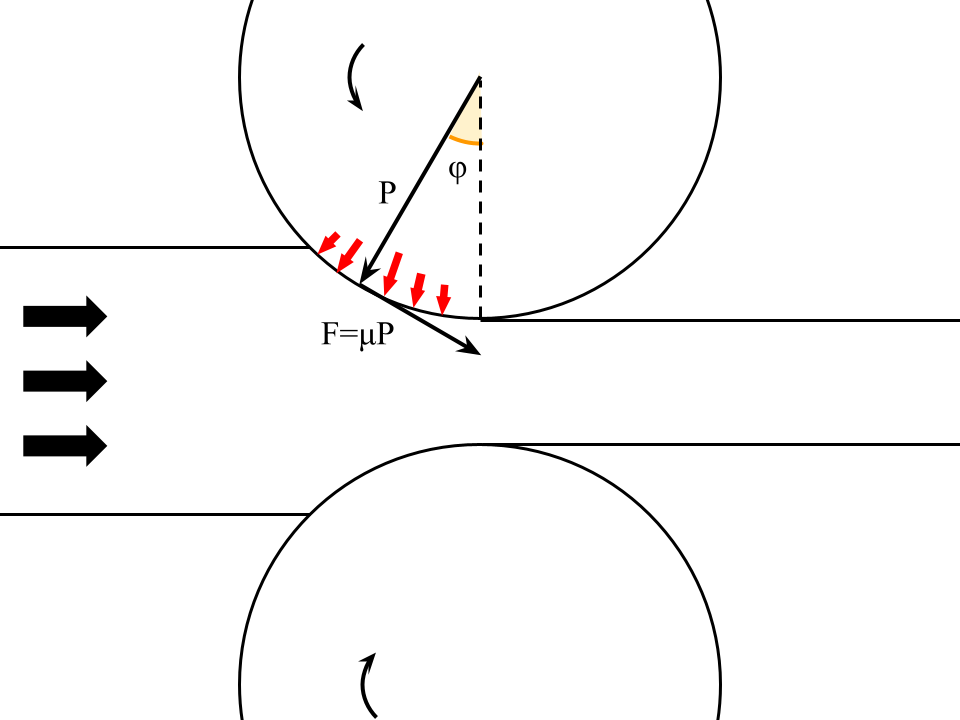
9. 2차원 직교 절삭에서 전단각(φ)을 산출하는 식으로
가장 옳은 것은? (단, rc은 절삭비이고 α는 경사각이다.)
답 : ④
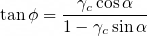
10. 고분자 섬유(또는 필라멘트) 제조에 대한 설명으로 가장 옳지 않은 것은?
① 용융체 스피닝(melt spinning)은 고분자 재료를 용융 상태로 가열해 방적돌기(spinneret)로 압출하는 것이다.
② 용융체 스피닝 시 방적돌기를 떠난 섬유(필라멘트)는 물속에서 냉각된다.
③ 건식 스피닝(dry spinning)을 위한 원자재는 용액 상태이다.
④ 습식 스피닝(wet spinning)을 위한 원자재는 용액 상태이다.
답 : ②
용융체 스피닝 시 방적돌기를 떠난 섬유(필라멘트)는 공기 중에서 냉각된다.
고분자 섬유(필라멘트) 제조 과정
1. 중합 공정 - 단량체(monomer)을 이용하여 고분자로 만드는 과정. 중합 반응을 이용한다. 괴상 중합, 용액 중합, 현탁 중합, 계면 증축합, 유화 중합 등의 방식이 있다. 소광제 TiO2를 첨가하여 광택을 줄여준다.
2. 방사 공정 - 중합된 고분자를 건조, 용융, 연신, 냉각하는 과정이다.
1) 용융방사(melt spinning) : 고분자의 융점 이상의 온도에서 용융시키고 방적돌기(spinneret)로부터 압출한 후 냉각 공기 속을 통과시켜 고화시킨 후 권취 공정을 통과하여 가늘고 긴 모양의 섬유가 얻어진다. 나일론과 폴리에스터의 제조에 쓰인다.
2) 건식방사(dry spinning) : 섬유 고분자를 쉽게 증발할 수 있는 용매에 녹인 용액을 뜨거운 공기 속으로 압출하고 용매를 증발시켜 섬유상으로 고화시키는 방법이다. 아세테이트, 아크릴, 폴리염화비닐섬유 등의 제조에 쓰인다.
3) 습식방사(wet spinning) : 섬유 고분자를 용매에 용해시켜 방사 원액을 만들고 이것을 방사구를 통해 압출시키면 재생, 응고되어 고화된다. PVA, 폴리염화비닐(PVC) 등의 제조에 이용된다.
11. 고온에서 작업함으로써 줄일 수 있는 제조공정의 결함으로 가장 옳은 것은?
① 결정립성장 - 오렌지필(orange peel)
② 압출 - 속도균열(speed cracking)
③ 굽힘 - 스프링백(springback)
④ 절삭가공 - 크레이터마모(crater wear)
답 : ③
① 오렌지필(orange peel) : 금속 판재를 딥드로잉하면 연신부 표면이 귤껍질처럼 거칠게 나타나는 현상. 결정립이 클수록, 온도가 높을수록 잘 발생한다.
② 압출 속도가 너무 높으면 표면 온도가 급격히 상승하여 표면 균열이 발생한다. 빌렛 온도와 압출속도를 낮춤으로써 방지할 수 있다.
③ 스프링백은 굽힘 가공 시 고온에서 작업함으로써 줄일 수 있다.
④ 크레이터마모의 원인은 고온에 의한 확산이다.
12. <보기>에서 설명하는 플라스틱 재료로 가장 가까운 것은?
<보기> 열경화성 플라스틱이다. 취성이 있다. 강성이 높고 치수안전성이 있다. 열, 전기, 화학물 등에 대한 저항성이 높다.
① 아크릴(acrylics)
② 폴리프로필렌(polypropylene)
③ PVC(polyvinyl chloride)
④ 페놀수지(phenolic)
정답 : ④
페놀수지에 대한 설명이다.
아크릴, 폴리프로필렌, PVC는 열가소성 플라스틱이다. →열가소성/열경화성 여부만으로 선지소거 가능함.
13. 용접부의 용입 부족(incomplete penetration)을 방지할 수 있는 방법으로 가장 옳은 것은?
① 열유입량을 감소시킨다.
② 용접부 설계는 변경하지 않는다.
③ 용접 중에 용접 속도를 감소시킨다.
④ 접합하고자 하는 면이 서로 교차하도록 조절한다.
정답 : ③
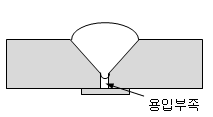
용입부족은 용접전류 증가, 열유입량 증가, 설계 변경, 용접속도 감소 등으로 해결할 수 있다.
14. 전해연삭(electrochemical grinding)에 대한 설명 으로 가장 옳지 않은 것은?
① 전해 작용에 의해 가공물 표면에 생기는 양극 생성물을 연삭 숫돌로 제거하는 가공법이다.
② 전해 작용에 의한 가공이 대부분이며, 연삭에 의한 재료 가공량은 매우 적은 편이다.
③ 전해 연삭용 숫돌은 전도성의 숫돌 입자와 절연성의 결합제로 제작된다.
④ 가공 중 발열량이 적어 가공 경화가 나타나기 쉬운 재료의 가공에 적합하다.
답 : ③
전해연삭에서 숫돌은 전도성의 숫돌 입자와 전도성의 결합제를 사용한다.
방전가공 : 절연성 방전액 사용
전해가공 : 전도성 가공액 사용
전해연삭 : 전도성 숫돌, 결합제 사용
15. 불활성 가스 아크 용접의 일종인 TIG 용접에 대한 설명으로 가장 옳지 않은 것은?
① 소모성의 텅스텐(tungsten) 전극을 사용한다.
② 가스 텅스텐 아크 용접(GTAW : Gas Tungsten Arc Welding)이라고도 한다.
③ 직류 전원 사용 시 정극성에서는 모재가 더 많이 가열 되므로 용입이 깊다.
④ 별도의 용가재(filler metal)를 용접부에 공급하여야 한다.
답 : ①
TIG 용접은 비소모성 전극을 사용한다.
16. 연삭 시 결합도가 높은 숫돌(단단한 숫돌)을 사용해야 할 조건에 해당하는 것은?
① 연질 재료를 연삭할 때
② 숫돌바퀴의 원주 속도가 빠를 때
③ 연삭 깊이가 깊을 때
④ 숫돌과 소재의 접촉 면적이 클 때
답 : ①
결합도가 높은 숫돌 - 연질 재료, 저속, 연삭깊이가 작을 때, 접촉면적이 작을 때, 표면이 거칠 때
결합도가 낮은 숫돌 - 경질 재료, 고속, 연삭깊이가 클 때, 접촉면적이 클 때, 표면이 치밀할 때
17. <보기>는 센터리스 연삭(centerless grinding) 방식 중 통과 이송(through feed) 연삭 방식을 나타낸 그림이다. 조정숫돌의 지름을 D [mm], 조정숫돌의 분당회전수를 N [rpm], 연삭숫돌 중심축과 조정숫돌 중심축 사이의 각도를 θ라 하면, 공작물이 숫돌 사이를 통과하는 속도 f [mm/min]를 구하는 식으로 가장 옳은 것은?
답 : ①
통과이송법의 공식

18. 분말야금공정의 소결(sintering) 공정에 대한 설명 으로 가장 옳은 것은?
① 분말이 공정 중 온전히 고형의 상태를 유지한다.
② 소결 시 제품의 밀도가 다소 감소한다.
③ 생형밀도가 높은 분말을 사용하는 것이 치수정도 유지에 유리하다.
④ 소결 온도가 높을수록 소결 후 제품의 연신율이 감소한다.
답 : ③
① 소결 공정 중 일부 낮은 융점을 가지는 물질에 의한 액상이 형성되어 이 액상 물질에 의해 물질이동이 빠르게 일어나고 입자 간 빈 공간에도 스며들어 치밀하게 된다. 이를 액상소결이라고 한다.
② 소결 시 제품의 원자간의 결합으로 인해 재결정이 일어나며 강도와 밀도가 증가한다.
④ 소결 온도가 높을수록 소결 후 제품의 인장강도와 연신율이 증가한다.
※분말야금공정
- 가공단계 : 분말제조-입도선별-혼합-압축생형-소결
- 압축생형 : 소결하기 전 분말을 혼합 및 압축한 상태.
- 패킹지수 : 용적밀도(공기와 수분 포함)/진밀도(입자만의 밀도)의 값. 약 0.5~0.7
- 소결온도 : 용융점의 약 70~90%
- 소결기구 : 확산, 증기상 재료이동, 스파크소결
19. X-선 리소그래피와 포토리소그래피에 대한 설명으로 가장 옳지 않은 것은?
① X-선 리소그래피는 포토리소그래피보다 해상도가 우수하다.
② X-선 리소그래피는 포토리소그래피보다 높은 종횡비 (high aspect ratio)의 구조물을 제작할 수 있다.
③ 광선의 회절량은 X-선 리소그래피가 포토리소그래피보다 크다.
④ 포토리소그래피에 비해 X-선 리소그래피는 고가의 생산설비를 사용한다.
답 : ③
광선의 회절량은 X-선 리소그래피가 포토리소그래피가 작다.
포토리소그래피는 현재 가장 많이 사용되는 방식으로, 비용이 작고 조작이 쉽다. 그러나 빛의 회절에 의해 해상도가 제한된다. 이를 개선하기 위해 전자 빔 리소그래피, 극자외선 리소그래피, X-선 리소그래피, 이온 빔 리소그래피 등의 방식이 개발중이다.
20. 4개의 날을 가지는 지름 20[mm]의 평엔드밀로 공작물을 절삭하려 한다. 절삭속도는 60[m/min], 날 당 이송 (feed per tooth)은 0.1[mm/tooth]인 조건으로 절삭 하려면 분당 주축 회전수 N [rpm]과 분당 이송속도 f[mm/min]의 값은? (단, π=3으로 계산한다.)
N f
① 1400 400
② 1400 100
③ 1000 400
④ 1000 100
답 : ③



'기출문제 해설 > [서울시 7급 기계공작법]' 카테고리의 다른 글
【기계공작법】2020 서울시 7급 기계공작법 해설 (0) | 2022.01.21 |
---|---|
【기계공작법】2019 서울시 7급 기계공작법 해설 (0) | 2022.01.21 |
【기계공작법】2018 서울시 7급 기계공작법 해설 (0) | 2022.01.20 |
【기계공작법】2017 서울시 7급 기계공작법 해설 (0) | 2022.01.19 |
【기계공작법】2016 서울시 7급 기계공작법 해설 (0) | 2022.01.18 |
댓글